Résolution de problèmes opérationnels
Comment ce fournisseur d’accès internet a rentabilisé ses opérations de la chaîne d’approvisionnement.
Cette entreprise est le deuxième câblodistributeur en Ontario et au Québec, et un leader canadien pour les services de télécommunication et de multimédia aux particuliers et aux entreprises.
Pour ce faire, l’entreprise gère une chaîne d’approvisionnement à partir d’entrepôts et d’opérations situées au Québec et en Ontario. Elle approvisionne des techniciens et vendeurs de l’entreprise en matériels et équipements nécessaires au déploiement du réseau et à fournir les services d’accès internet et télévision : box, kits de connexions, cables, connecteurs, etc..
À la suite d’un premier mandat stratégique pour réduire les couts de sa chaine d’approvisionnement, améliorer les délais de mise en service et la qualité, l’entreprise souhaitait passer du plan à l’action pour réaliser la transformation de sa chaîne d’approvisionnement. La première étape concernait ses opérations situées en Ontario qui traitaient essentiellement le retour des équipements reçus des abonnés, leur test, remise en état et remise en service et l’exécution de la politique tarifaire liée au changement de la situation de l’abonné.
Suite à un diagnostic détaillé de la performance de production actuelle, le mandat fût déterminé :
- Revoir l’aménagement de l’entrepôt principal et séparer les flux de valeur notamment production vs. stockage, retours usagés vs. neuf;
- Réviser les opérations de production réception-test-remise en etat-programmation-emballage;
- Créer des cellules de production performantes pour maitriser qualité, couts, délais dans des conditions de qualité de vie au travail, santé et sécurité des intervenants;
- Implanter flux tirés et le flux unitaire;
- Contrôler les niveaux de stocks et en-cours pour maitriser les délais;
- Introduire et formaliser le travail standard pour accroitre la qualité et les compétences;
- Gérer les fluctuations quotidiennes de demande pour fluidifier la production
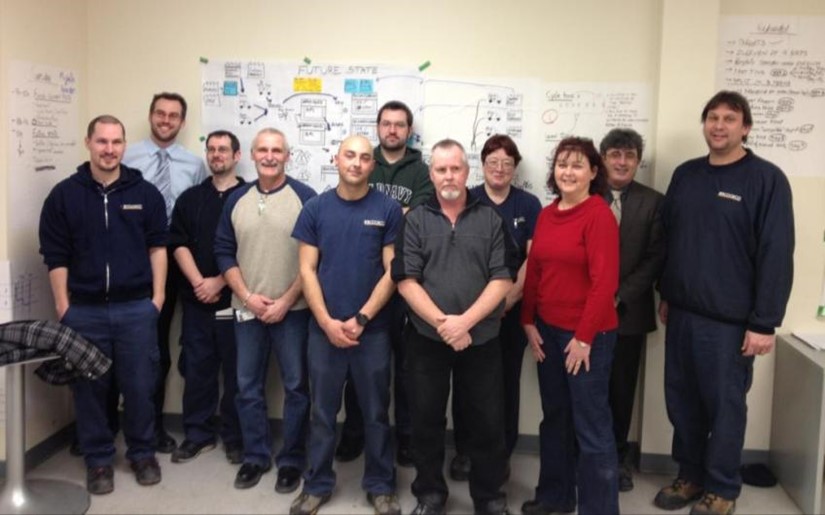
Dans ce cadre, les consultants avaient pour rôle
- Accompagner et orienter le directeur de projet interne;
- S’assurer que le directeur de projet applique les règles de l’art en Lean afin de lui délivrer son accréditation « ceinture noire » au cours du projet;
- S’assurer de l’adaptation du matériel de formation aux besoins particuliers du client;
- Résoudre des problèmes particuliers notamment concernant la gestion du changement (voir plus loin);
- Obtenir des changements au processus d’approbation de dépenses en immobilisation afin de l’adapter au cadre de gestion Lean;
- Mener un atelier intensif Kaizen de cinq jours avec une équipe terrain intégrant toutes les compétences métier (logistique, test des équipements, remise en état, etc.), comprenant :
- Cartographie des états actuels et futurs de la chaîne de valeur;
- Identification des gaspillages et irritants à l’origine des problèmes de performance;
- Révision du flux de production et mise en œuvre des cellules de travail;
- Révision des processus matériels et d’information en soutien à la production;
- Contrôler et accompagner la mise en œuvre dans les règles de l’art pour réaliser le mandat;
- Accompagner et aider l’équipe du client à passer du projet à la production permanente dans les nouvelles conditions optimisées.

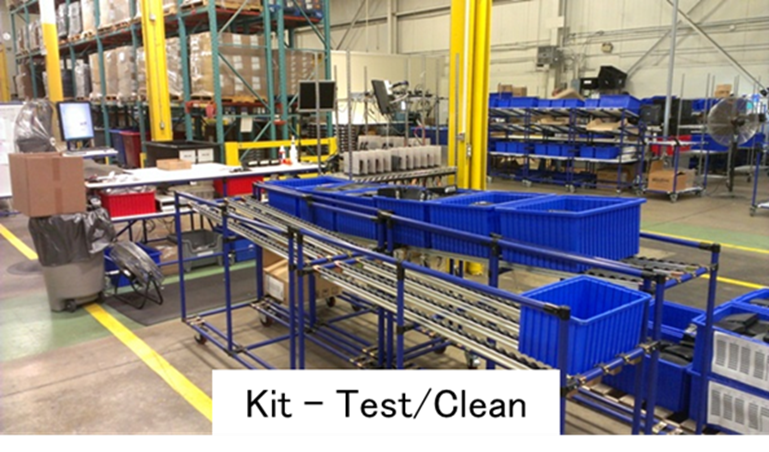
Résultats atteints :
- Réduction de 55 % de l’espace de production (moins 900 m2);
- Augmentation de 37 % de la productivité, permettant de diminuer drastiquement le recours à la main-d’œuvre intérimaire (de 16 postes intérimaires à 6);
- Réduction de 44 % (de 9 à 5 jours) du temps de livraison au client interne;
- Résolution de problèmes : processus optimisés permettant l’élimination de 31 problèmes, gaspillages, rsques pour la sané et la sécuritéé et irritants récurrents;
- Mise en œuvre des bonnes pratiques Lean de contrôle de la qualité (gestion des rebuts, des retouches, diminution des défauts).
Le chef de projet interne a déclaré, lors de la présentation des résultats au comité de pilotage stratégique, constitué entre autres du Vice-Président de la chaine d’approvisionnement de l’entreprise :
“Ce premier atelier de travail Kaizen représente le fondement de la nouvelle culture LEAN dans l’entreprise. Nous avons jeté les bases d’un nouveau départ et, comme les blocs lego eux-mêmes, les futures initiatives Lean peuvent s’appuyer sur celui-ci et s’interconnecter avec celui-ci.”
Faire face à la résistance du personnel
« À l’époque, personne ne savait si nous étions productifs ou non parce que nous n’avions aucun moyen de mesurer et nous ne pouvons pas améliorer quelque chose que nous ne mesurons pas » explique B.J., directeur des entrepôts de l’entreprise. »
Le processus de changement était très intense – à un point tel que certains membres du personnel prirent les constats personnellement. « Notre personnel de longue date faisait les choses de la même façon depuis plusieurs années et réalisaient qu’on pouvait faire différemment…avec plus d’efficacité»
Les gens étaient sur la défensive et se sentaient attaqués. Ils voulaient prouver que leur méthode était la bonne et que le nouveau processus ne fonctionnerait pas. L’équipe de l’entreprise a fini par surmonter cette difficulté, mais il a fallu une bonne année pour voir un véritable changement de culture.
Après avoir pris du recul, les Directeurs admettent sans détour qu’on doit s’attendre à un énorme choc culturel. Jusqu’à ce que les travailleurs reconnaissent les avantages et qu’ils valident le nouveau processus, il y aura beaucoup de résistance.
« Nous, en tant qu’équipe de direction, n’en étions même pas convaincus », avoue le chef de l’entrepôt. Maintenant, les deux sont d’accord pour dire qu’une équipe de gestion doit avant tout être unie. Puis, les gestionnaires doivent avoir une idée claire des bénéfices générés par la fabrication Lean afin de bien vendre le changement à leur équipe.
Le chef de l’entrepôt ajoute que « les leaders doivent croire au Lean et y adhérer à 100 %. Et tant que vous ne passerez pas cette étape cruciale, il n’y aura aucun changement. »
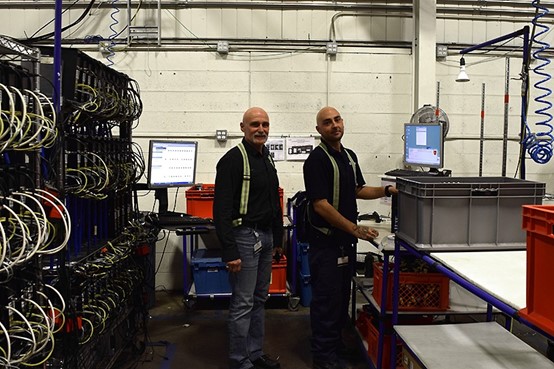
Réduire les gaspillages du transport et du mouvement
L’entreprise a vu son niveau de productivité augmenter considérablement dans l’année suivant l’intégration des méthodes lean.
Avec les nouveaux procédés, les employés se concentrent sur la réduction des gaspillages de mouvement et de transport dans l’atelier de production et dans l’entrepôt. Pour ce faire, l’équipe réduit au minimum les mouvements en reconfigurant l’aménagement de l’atelier de production et en utilisant des chariots modulaires à gravité sur mesure adaptés à leurs besoins. Fini l’époque où les appareils parcouraient une distance équivalent 3 terrains de football dans une usine de 1000 m2!
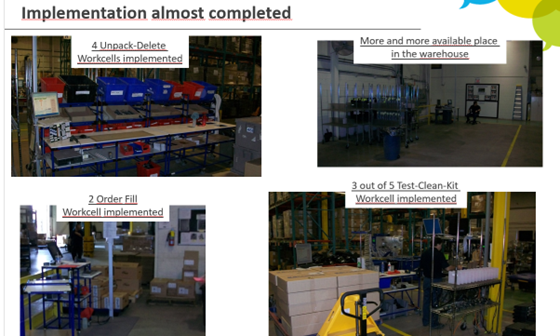
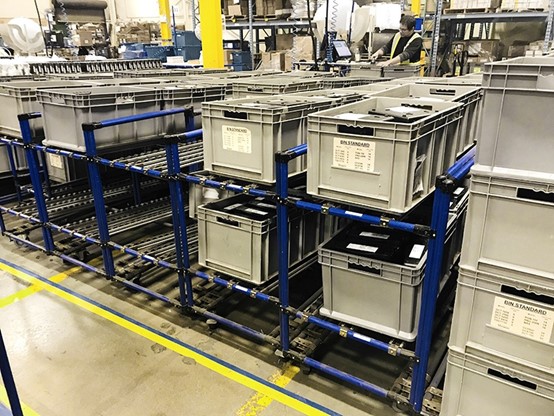